Research
Patrik Axelsson's research is about sensor fusion and control for industrial robots. The problems are:-
Estimate the position of the end-effector using an accelerometer attached to the end-effector. The motivation for estimating the position of the end-effector is presented below. The position is estimated using Bayesian techniques for state estimation, here represented by the extended Kalman filter and the particle filter. The estimation of the position has been evaluated using both simulated and experimental data. Three sub-problems have been investigated to get a good estimate of the position:
- Estimating the covariance matrix for the process noise. The proposed method uses the expectation maximisation algorithm and the extended Kalman smoother.
- Estimating the orientation and position of the accelerometer mounted on the robot. The orientation is obtained using static experiments and the position is obtained from measurements where the robot moves with constant speed.
- Sampling methods for continuous-time systems. The focus has been to do the time update of the (extended) Kalman filter in continuous time instead of discretising the model. As a result, a solution of the continuous-time differential Lyapunov equation has been proposed.
- Improve the control performance of the manipulator using different control strategies. Two strategies have been investigated:
- Improve the control performance of the industrial manipulator using different kind of sensors, such as accelerometers, combined with H-infinity robust controllers
- Use of the estimated quantities together with iterative learning control (ILC). The norm-optimal ILC method has been modified to handle both the mean and covariance of the estimated quantities.
Motivation
The first industrial robots were big and heavy with rigid links and joints. The development of new robot models has been focused on increasing the performance along with cost reduction, safety improvement and introduction of new functionalities. One way to reduce the cost is to lower the weight of the robot which conduces to lower mechanical stiffness in the links. Also, the components of the robot are changed such that the cost is reduced, which can infer larger individual variations and unwanted nonlinearities. The most crucial component, when it comes to flexibilities, is the gearbox. The gearbox has changed more and more to a flexible component described by nonlinear relations, which cannot be neglected in the motion control loop. The friction in the gearbox is also an increasing problem that is described by nonlinear relations. The available measurements for control are the motor angular positions, but since the end-effector, which is the desired control object, is on the other side of the gearbox it cannot be controlled in a satisfactory way. Instead, extensive use of mathematical models describing the nonlinear flexibilities are needed in order to control the weight optimised robot. What if the tool position is available for control? Is it possible to achieve a good enough control performance?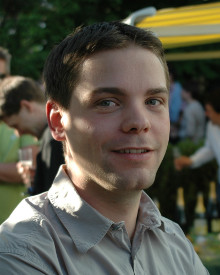
Doktorand i reglerteknik
- Telefon:
- +46 13 28 13 65
- E-post:
- axelsson@isy.liu.se
- Adress:
- Inst. för systemteknik
- Linköpings universitet
- 581 83 Linköping
- Besöksadress:
- Campus Valla
- B-huset
- Rum 2A:529 (i A-korridoren på bottenvåningen mellan ingång 25 och 27)
Informationsansvarig: Patrik Axelsson
Senast uppdaterad: 2014-04-03